Mastering Welding WPS Standards: Best Practices and Techniques for Top Quality Welds
In the world of welding, mastering Welding Treatment Spec (WPS) criteria is a critical component that straight influences the high quality and honesty of welds. As we navigate with the ins and outs of welding WPS requirements, revealing key understandings and methods for accomplishing top-tier welds will certainly be vital for welders seeking to stand out in their craft and generate welds that stand the examination of time.
Understanding Welding WPS Requirements
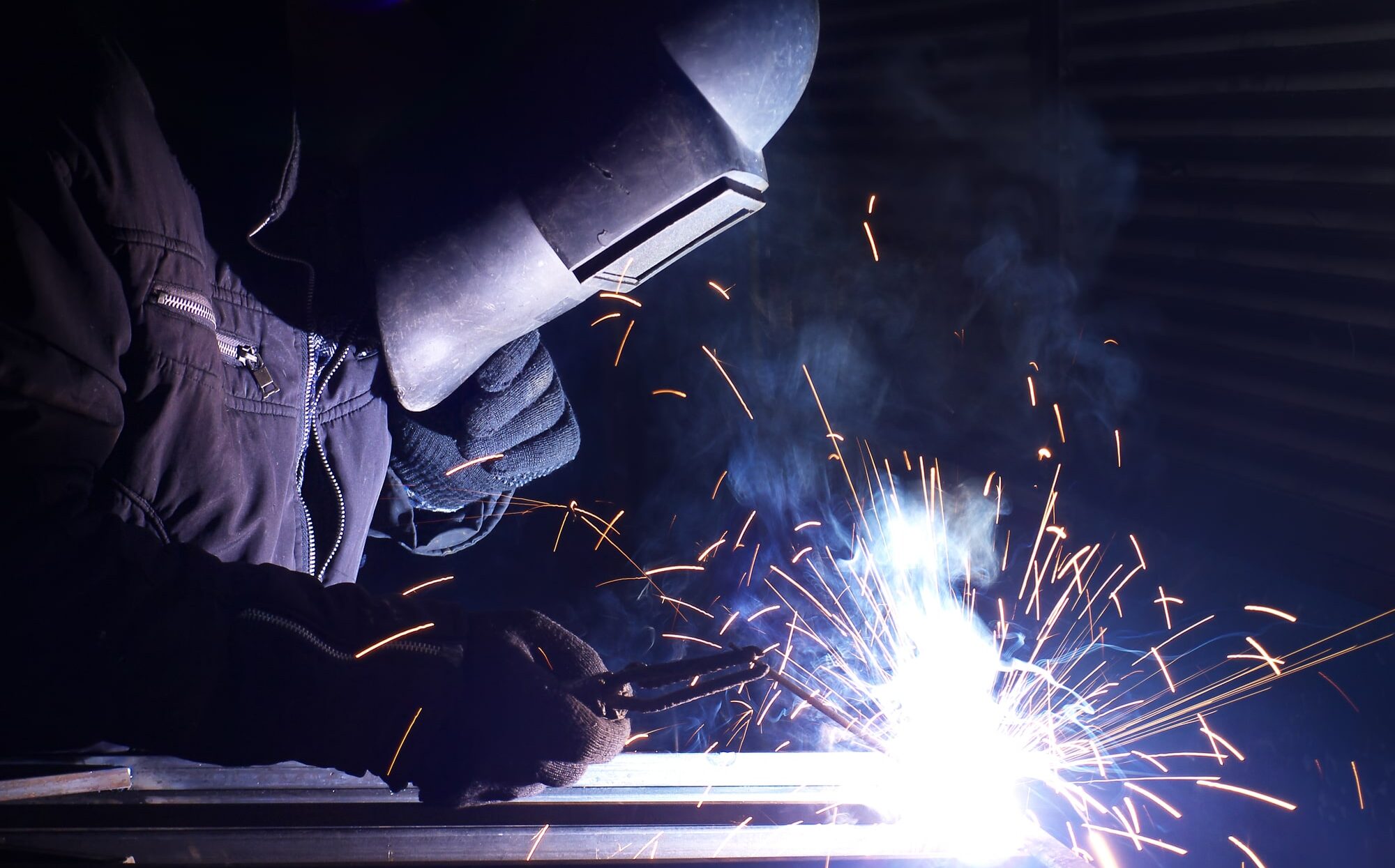
Inspectors depend on WPS documentation to validate that welding treatments are being adhered to appropriately and that the resulting welds are of high top quality. Engineers use WPS criteria to make welding procedures that make sure the toughness and reliability of welded structures.
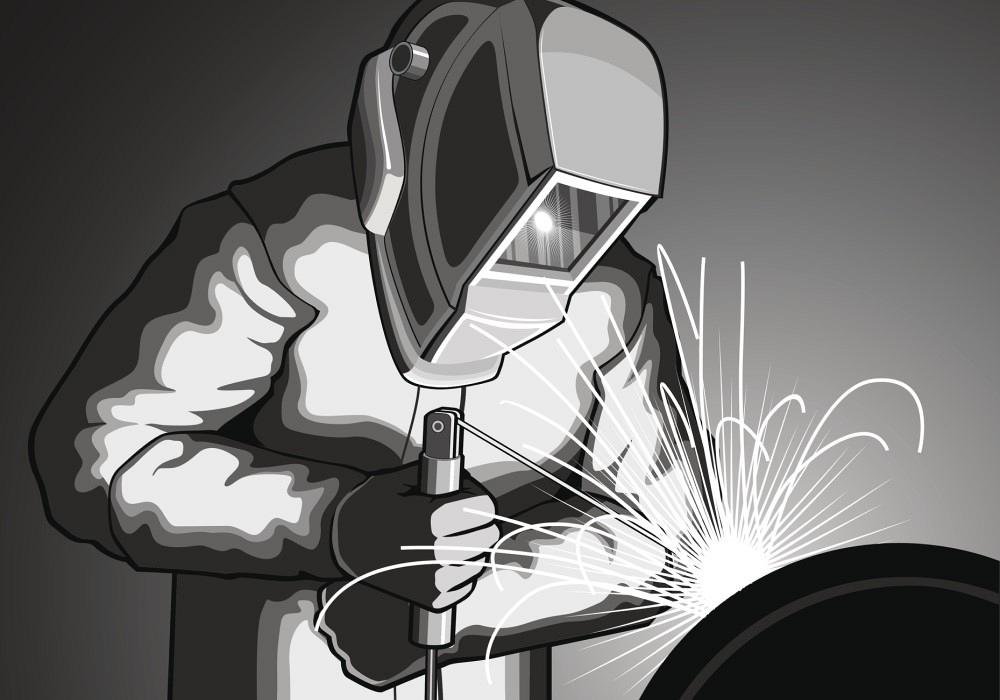

Important Tools for Quality Welds
Understanding welding WPS criteria is important for welders to efficiently make use of the necessary devices required for generating high quality welds. The type of welding device needed depends on the welding procedure being used, such as MIG, TIG, or stick welding. Cord brushes and cracking hammers are vital for cleaning up the weld joint before and after welding to get rid of any type of impurities that might affect the high quality of the weld.
Secret Methods for Welding Success
To achieve welding success, one should master the vital methods necessary for generating high-grade welds. Keeping a steady welding and a consistent hand placement throughout the process is key to attaining precision and uniformity in the welds. By understanding these crucial techniques, welders can elevate the quality of their job and achieve welding success.
Ensuring Conformity With WPS Requirements
Additionally, keeping thorough documents of welding specifications, equipment calibration, and inspection results is critical for showing compliance with WPS standards. By diligently sticking to WPS requirements, welders can guarantee that their work fulfills the needed top quality levels and adds to the overall success of the welding project.
Troubleshooting Common Welding Issues
To address this, making sure proper cleaning of the base metal prior to welding and making use of the appropriate securing gas can significantly decrease porosity. Furthermore, distortion, fracturing, and spatter are common welding challenges that can be reduced with correct joint prep work, consistent heat control, read the full info here and selecting the suitable welding consumables. By completely recognizing these usual welding problems and their origin triggers, welders can effectively troubleshoot problems and accomplish premium welds.
Final Thought
In verdict, understanding welding WPS criteria calls for a thorough understanding of the guidelines, utilizing important tools, and executing essential techniques for successful welds. Guaranteeing compliance with WPS standards is essential for producing quality welds and staying clear of usual welding concerns. By adhering to best methods and techniques, welders can accomplish trusted and constant outcomes in their welding projects.
In the world of welding, grasping Welding Treatment Requirements (WPS) criteria is a vital element that straight influences the high quality and integrity of welds.When diving into the realm of welding practices, a critical element to comprehend is the significance and intricacies of Welding Treatment Spec (WPS) standards. WPS criteria supply an in-depth guideline for welding procedures, making sure consistency, top quality, and security in the welding process. The kind of welding maker needed depends on the welding procedure being used, such as MIG, TIG, or stick welding.Attaining welding success with the mastery of vital methods demands a complete understanding and index adherence to Welding Procedure Requirements (WPS) requirements.